What is Lean?
Discover what-is-lean, its principles, and benefits. Learn how lean manufacturing boosts efficiency and reduces waste.
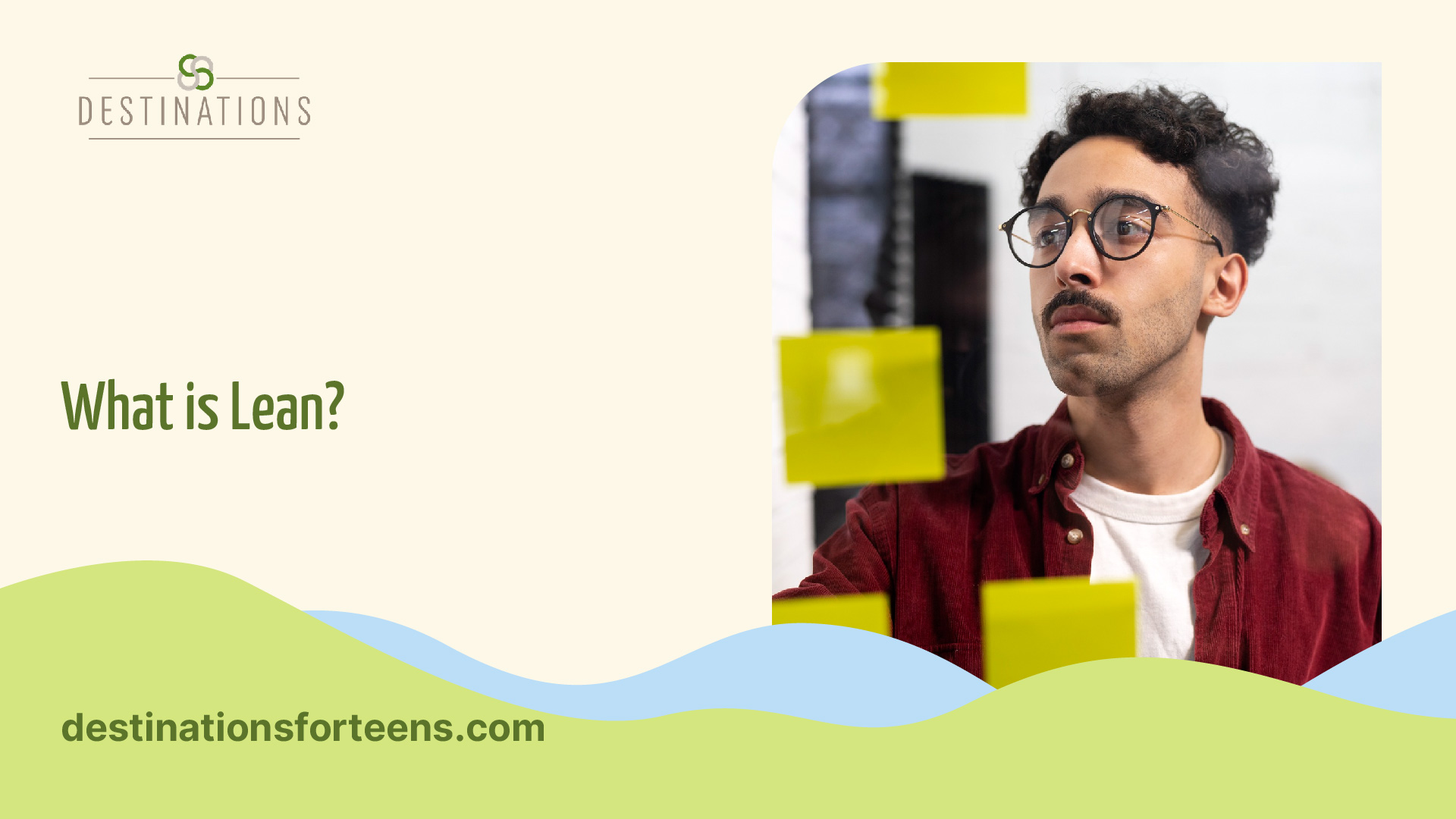
Understanding Lean Principles
Lean principles form the bedrock of strategies designed to eliminate waste and enhance operational efficiency across various sectors. These principles help companies refine their processes to deliver maximum value to customers.
Foundation of Lean
Lean is built on a foundation of principles aimed at eliminating waste and improving business operations. The core idea is to create more value for customers with fewer resources by optimizing the way work gets done. This is achieved by focusing on what adds value from the customer's perspective and systematically reducing anything that does not.
Lean's foundation can be traced back to the Toyota Production System, which revolutionized manufacturing by introducing a systematic approach to waste reduction and continuous improvement. This approach, known as Kaizen, emphasizes small, incremental changes that collectively lead to significant improvements.
Lean Manufacturing Basics
Lean manufacturing focuses on minimizing waste within manufacturing systems while maximizing productivity. Waste is defined as anything that customers do not believe adds value and are not willing to pay for.
The basic principles of lean manufacturing include:
These principles were introduced to the Western world in 1990 through the publication of "The Machine That Changed the World," which detailed Toyota's lean production system.
Understanding the foundation and basics of lean manufacturing sets the stage for exploring its core principles, methodologies, and benefits. By focusing on value creation and waste reduction, lean principles provide a roadmap for organizations to enhance their efficiency and deliver greater value to customers.
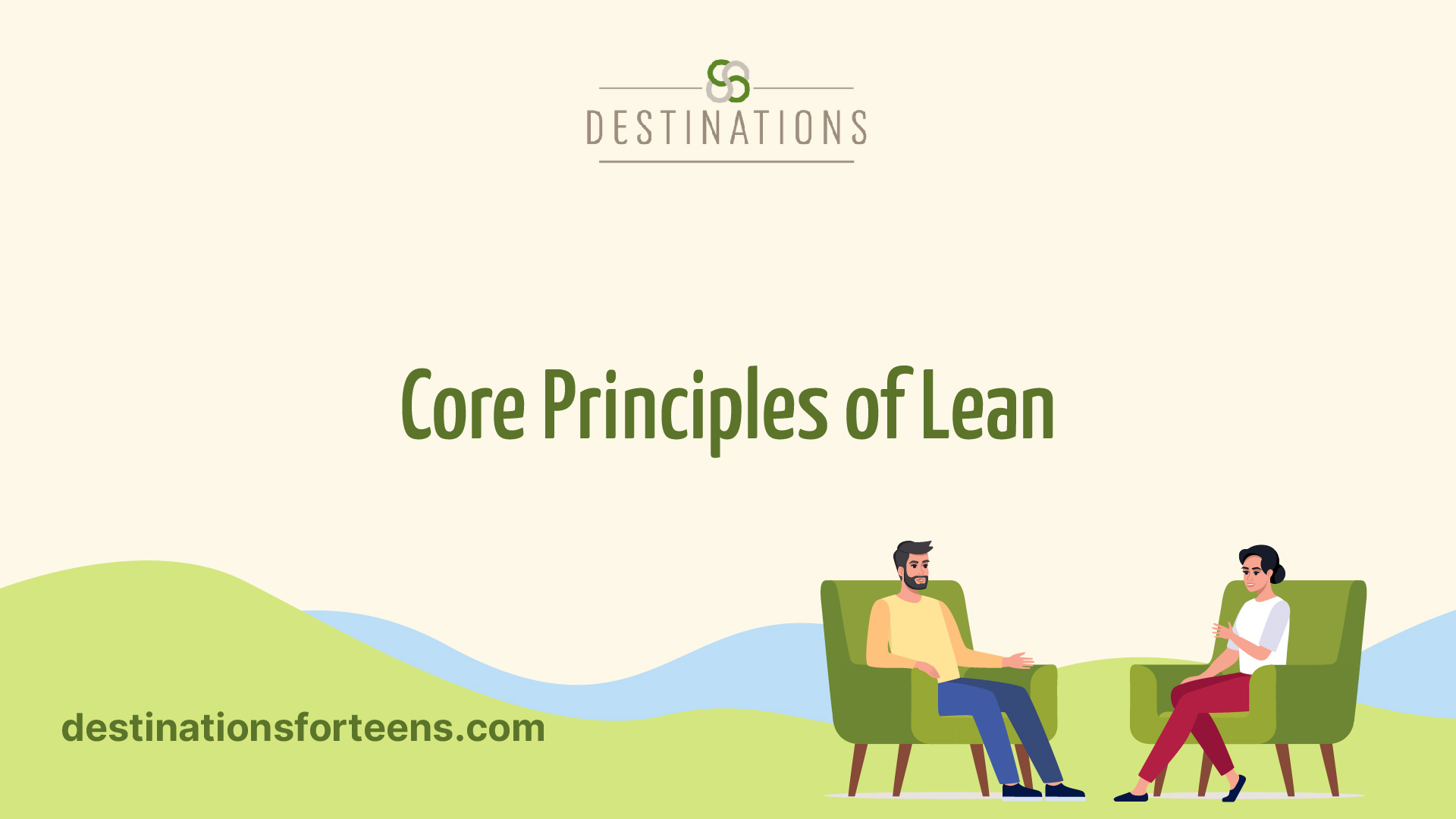
Core Principles of Lean
Lean principles are foundational to creating efficient and waste-free production processes. Key among these principles are Kaizen and the Toyota Production System, both of which have significantly shaped the Lean methodology.
Kaizen and Continuous Improvement
Kaizen, a Japanese term meaning "change for the better," is a core concept in Lean manufacturing. It emphasizes continuous improvement, where small, incremental changes are made to processes to enhance efficiency and eliminate waste. This principle encourages everyone in the organization, from top management to frontline workers, to contribute ideas for improvement.
Kaizen involves several practices:
This methodology not only improves operational efficiency but also boosts employee engagement and morale by valuing their input and promoting a culture of collective responsibility.
Toyota Production System Influence
The Toyota Production System (TPS) is the blueprint for Lean manufacturing. Introduced to the Western world through the publication of The Machine That Changed the World, TPS revolutionized the way companies approached production by emphasizing efficiency, waste reduction, and continuous improvement.
Key elements of TPS include:
The five core principles of Lean, inspired by TPS, are:
The influence of TPS on Lean principles is profound, providing a structured yet flexible framework for achieving operational excellence. By integrating Kaizen and the Toyota Production System, organizations can create a robust culture of continuous improvement and efficiency.
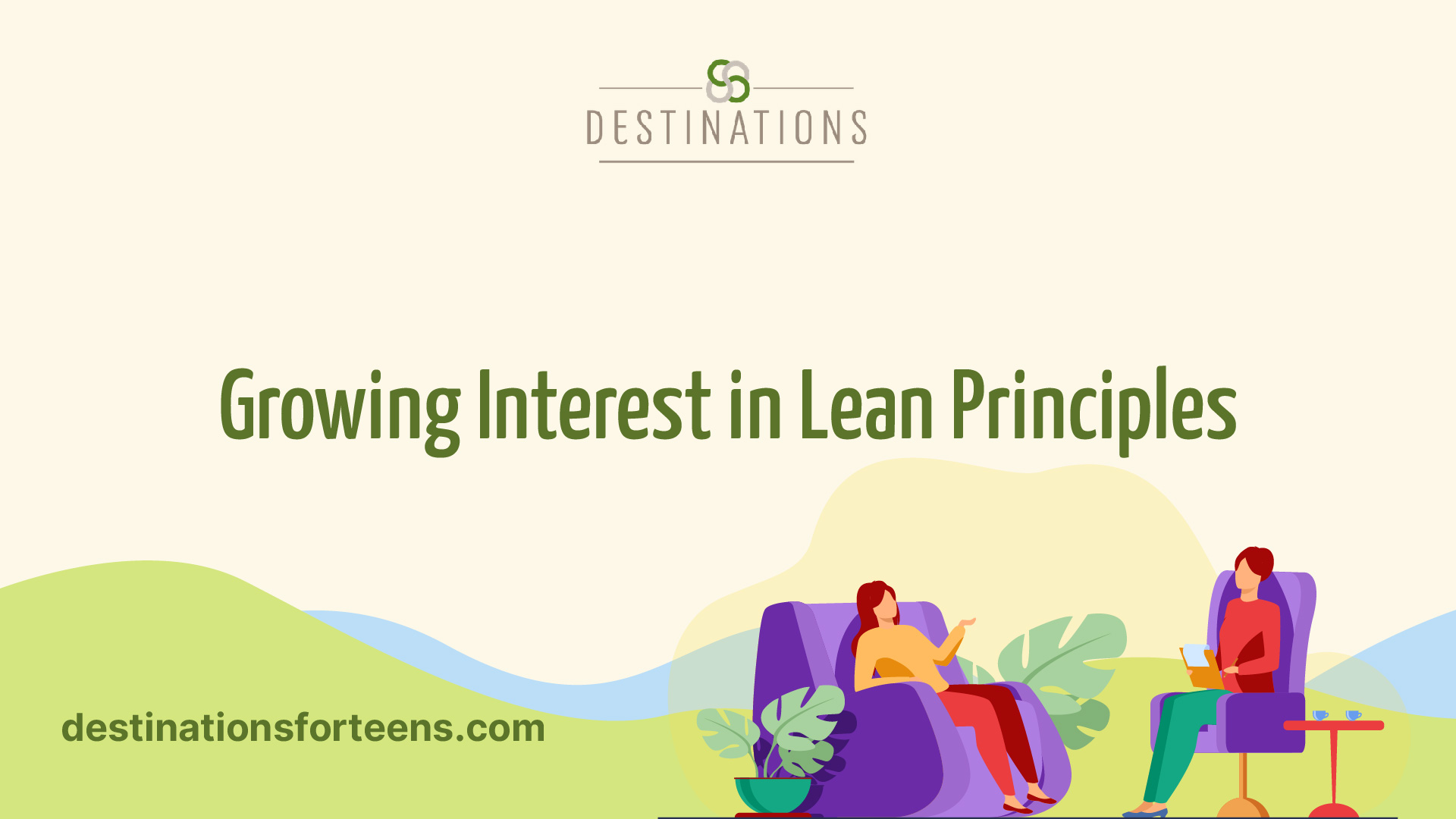
Lean Implementation
Lean implementation has seen significant evolution and adaptation across various industries since its inception. This section explores the origins and practical applications of lean principles.
Lean Manufacturing Evolution
Lean manufacturing, initially introduced to the Western world in 1990 through the publication of "The Machine That Changed the World," detailed Toyota's innovative lean production system. This system, known as the Toyota Production System (TPS), was developed between 1937 and 1962 and marked a significant milestone in lean history.
The TPS emphasized the elimination of waste, continuous improvement (Kaizen), and respect for people. Over time, these principles were distilled into five core lean principles as described in the book "Lean Thinking" (1996) by James P. Womack and Daniel T. Jones.
YearMilestoneReference1937-1962Development of Toyota Production System (TPS)Wevalgo1990Publication of "The Machine That Changed the World"TechTarget1996Publication of "Lean Thinking"Lean.org
Principles in Action
The application of lean principles has extended far beyond manufacturing. Lean thinking, which aims to maximize value while minimizing waste, has been adapted to various sectors including logistics, distribution, services, retail, healthcare, construction, maintenance, and government.
By following the five core principles—Value, Value Stream, Flow, Pull, and Perfection—organizations are able to streamline operations, enhance efficiency, and deliver greater value to customers. Toyota, a leading lean exemplar, demonstrates the success and power of lean enterprise, positioning itself as one of the largest automakers in the world.
In practice, implementing lean involves:
Lean implementation is a dynamic and evolving process, requiring commitment and adaptation to the unique needs of each organization.
Lean Methodologies
Lean methodologies are central to implementing Lean principles effectively in any organization. They are built on two fundamental ideas: respect for people and pursuing perfection.
Respect for People
Respect for people is a cornerstone of Lean management. This principle emphasizes the importance of valuing and empowering every individual within the organization. Employees closest to the processes often have the best insights into potential improvements. Lean encourages giving these individuals a voice in the improvement work.
Respect for people involves:
This principle fosters a culture where every team member feels valued and motivated to contribute to continuous improvement.
Pursuing Perfection
Pursuing perfection is the fifth principle in Lean manufacturing. This principle involves making continuous process improvement a part of the organizational culture. The goal is to strive for perfection by constantly reducing waste and improving quality.
Key aspects include:
Popular Lean methodologies that support this principle include:
By incorporating these methodologies, organizations can create a culture of excellence where every employee strives towards perfection.
Lean MethodologyDescriptionStandard WorkDocumenting best practices for consistency.PDSA CycleA method for continuous improvement.Kanban BoardsVisual tools for managing workflow.
These Lean methodologies are essential for driving continuous improvement and achieving operational excellence in any organization.
Lean Management Expansion
From Manufacturing to Various Sectors
Lean thinking has evolved significantly since its inception, extending its reach well beyond manufacturing. Leaders and organizations across various sectors have adapted Lean tools and principles to enhance efficiency and reduce waste in their respective fields. According to Lean.org, these sectors include logistics, distribution, services, retail, healthcare, construction, maintenance, and government.
SectorKey Lean ApplicationLogisticsStreamlining supply chain operationsDistributionReducing inventory levels and lead timesServicesEnhancing customer service processesRetailOptimizing stock management and merchandisingHealthcareImproving patient care and operational efficiencyConstructionMinimizing project delays and material wasteMaintenanceEnhancing equipment uptime and reliabilityGovernmentStreamlining administrative processes
The adoption of Lean principles in these sectors demonstrates the versatility and effectiveness of Lean methodologies in driving improvements across diverse environments. By focusing on efficiency and waste reduction, Lean thinking supports organizations in delivering better products and services at lower costs, ultimately creating more value for customers and stakeholders.
Growing Interest in Lean Principles
The growing interest in Lean principles among senior managers and leaders across various sectors reflects a broader recognition of the benefits that Lean methodologies offer. As noted by Lean.org, Lean consciousness and methods are beginning to take root among leadership teams, indicating a shift towards a more systematic and efficient approach to operations.
One notable example of Lean principles being applied outside traditional manufacturing is the adoption of Agile development in the software industry. This approach, which grew out of the need to manage product creation cycles more effectively, emphasizes iterative and incremental development. Agile development saves time and resources by focusing on building only the most essential functionality, thereby reducing waste and improving efficiency.
The expansion of Lean principles into various sectors underscores the adaptability and relevance of Lean thinking in today's competitive landscape. By embracing Lean methodologies, organizations can achieve continuous improvement, optimize their operations, and remain agile in response to changing market demands.
Lean Manufacturing Benefits
Efficiency and Waste Reduction
Lean manufacturing is a systematic approach to improving efficiency and reducing waste in manufacturing processes. It focuses on creating more value for customers while using fewer resources. The key to Lean Manufacturing lies in identifying and eradicating waste, often referred to as "muda" in Japanese. Waste can appear in various forms including overproduction, excess inventory, unnecessary motion, defects, waiting time, and underutilized talent [9].
By applying Lean principles, companies can significantly improve their operational efficiency. This includes reducing lead times, enhancing product quality, increasing productivity, and lowering costs. The ultimate goal is to maximize value creation for both customers and stakeholders [7].
Waste TypeDescriptionOverproductionProducing more than what is neededExcess InventoryHolding more stock than necessaryUnnecessary MotionExcessive movement by workersDefectsProducts that do not meet quality standardsWaiting TimeDelays in the production processUnderutilized TalentNot leveraging employee skills
Creating Value for Customers
Lean manufacturing is not just about efficiency; it is also about creating value for customers. By focusing on eliminating waste and optimizing processes, companies can offer better products and services at lower costs. This not only enhances customer satisfaction but also helps companies stay competitive in the market.
Lean methodologies emphasize the importance of agile operations that can swiftly respond to changes in customer preferences, market conditions, and technological advancements. This agility allows organizations to quickly adapt their production processes, reallocate resources, and pivot strategies to capitalize on emerging opportunities or mitigate risks.
BenefitDescriptionImproved Product QualityEnsuring products meet high standardsLower CostsReducing production and operational expensesEnhanced Customer SatisfactionMeeting and exceeding customer expectationsIncreased FlexibilityQuickly adapting to market changes
By implementing Lean principles, companies not only achieve operational excellence but also create a culture of continuous improvement and innovation. This culture ultimately leads to long-term success and sustainability in the competitive business landscape.
References
[2]:
[3]:
[4]:
[5]:
[6]:
[7]:
[8]:
[9]:
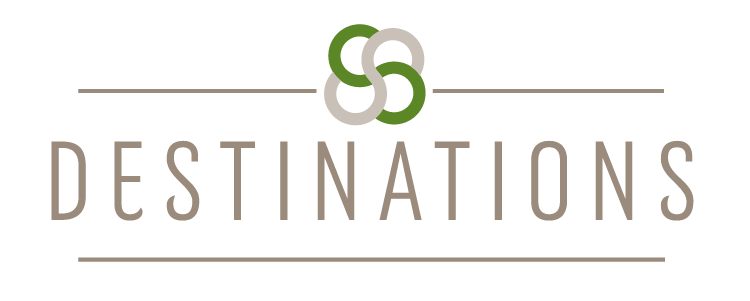
We Are Here To Help.
Call Us Today!
%201.png)
Subscribe To Our Mailing List
%201.png)